Koszt wytworzenia produktu to niezwykle ważny wskaźnik dla każdego przedsiębiorstwa produkcyjnego. Zobacz, jak możesz go obliczyć i co na niego wpływa.
Spis treści:
- Czym jest koszt wytworzenia produktu?
- Składniki kosztu wytworzenia produktu
- Kalkulacja kosztów bezpośrednich
- Kalkulacja kosztów pośrednich produkcji
- Jak technologia może pomóc w kalkulacji kosztów?
Najważniejsze informacje
- Koszt wytworzenia produktu to suma wydatków na produkcję, kluczowa dla ustalania cen i marż.
- W skład kosztów wchodzą wydatki bezpośrednie na materiały i pracę oraz pośrednie na zarządzanie i utrzymanie.
- Systemy ERP automatyzują kalkulację kosztów, zwiększając efektywność finansową przedsiębiorstw.
Czym jest koszt wytworzenia produktu?
Koszt wytworzenia produktu odgrywa ważną rolę w kształtowaniu cen, zarządzaniu zasobami oraz strategiach biznesowych w przedsiębiorstwie zajmującym się produkcją. Jest to suma wszystkich wydatków poniesionych na wyprodukowanie gotowego towaru, które mogą obejmować wiele czynników — od kosztów bezpośrednich pracy i materiałów,, po koszty pośrednie, takie jak amortyzacja urządzeń czy koszty zarządzania.
Znajomość jednostkowego kosztu wytworzenia produktu pozwala na ustalanie konkurencyjnych cen sprzedaży i identyfikację obszarów, w których możliwe jest obniżenie kosztów bez szkody dla jakości produktu. Dzięki temu firmy mogą poprawić swoje marże zysku i zwiększyć konkurencyjność na rynku.
Koszt wytworzenia produktu można podzielić na trzy główne kategorie:
- Koszty bezpośrednie — to wydatki bezpośrednio związane z produkcją, takie jak materiały bezpośrednie i bezpośredni koszt pracy. Są one łatwe do przypisania do konkretnego produktu i stanowią zasadniczą część kosztów produkcji.
- Koszty pośrednie produkcji — obejmują wydatki, które nie mogą być bezpośrednio przypisane do konkretnego produktu, ale są niezbędne dla procesu produkcyjnego, np. wynajem hali produkcyjnej, amortyzacja maszyn i urządzeń, czy koszty utrzymania personelu pomocniczego.
- Koszty ogólnego zarządzania — choć niezwiązane bezpośrednio z procesem produkcji, są niezbędne dla funkcjonowania przedsiębiorstwa jako całości, takie jak koszty administracyjne, marketingowe i inne.
Sprawne zarządzanie kosztem wytworzenia produktu może pozytywnie wpłynąć na konkurencyjność firmy, jej długoterminową stabilność oraz rozwój. Dlatego też, przedsiębiorstwa produkcyjne coraz częściej korzystają z zaawansowanych systemów zarządzania. Przykładem takiego rozwiązania jest enova365, które można wykorzystać jako system do analizy danych i optymalizacji kosztów (moduł Business Intelligence), ale także system do optymalizacji samych procesów produkcyjnych (moduł Produkcja).
Czytaj także: System ERP dla produkcji – sprawdź jak enova365 usprawnia zarządzanie produkcją
Składniki kosztu wytworzenia produktu
Jak wspomnieliśmy, składniki kosztu wytworzenia produktu można podzielić na trzy główne kategorie, z których każda ma bezpośredni wpływ na całkowity koszt produkcji i finalną cenę produktu.
1. Koszty bezpośrednie
- Materiały bezpośrednie — to surowce i podstawowe komponenty, które są integralną częścią wyprodukowanego towaru. Ich koszt jest bezpośrednio związany z ilością materiału zużytego na produkcję jednostkową produktu.
- Bezpośredni koszt pracy — to m.in. wynagrodzenia i inne świadczenia dla pracowników bezpośrednio zaangażowanych w proces produkcyjny. Często koszt ten zależy od czasu, który pracownicy poświęcają na produkcję jednostki produktu.
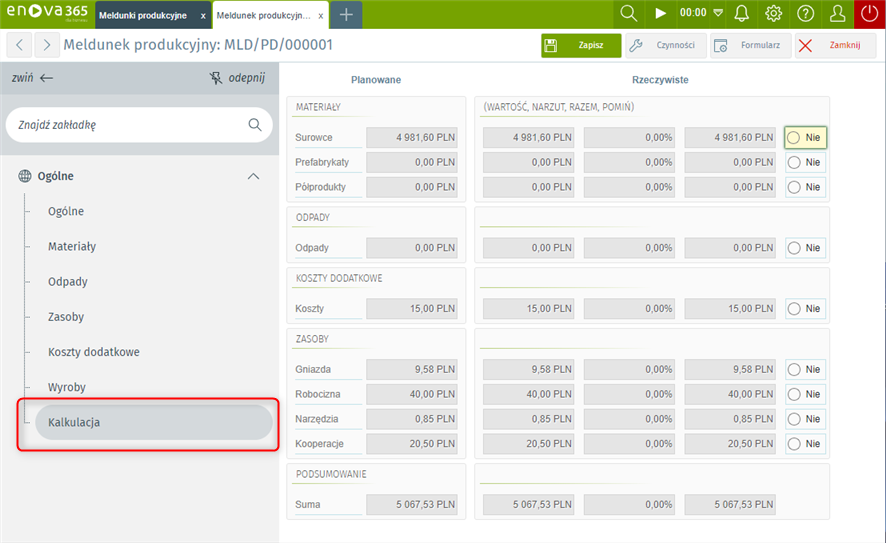
2. Koszty pośrednie produkcji
- Koszty ogólnego zarządzania produkcją — to wydatki związane z zarządzaniem procesem produkcyjnym, które nie mogą być bezpośrednio przypisane do poszczególnych jednostek produktu, np. pensje kierownictwa, koszty utrzymania biur.
- Amortyzacja — dotyczy stopniowego zużycia maszyn, urządzeń i budynków używanych w produkcji. Chociaż trudno jest przypisać ten koszt do pojedynczego produktu, jest on niezbędny do kalkulacji ogólnego kosztu produkcji.
- Koszty utrzymania i napraw — to m.in. bieżąca konserwacja i naprawy maszyn oraz urządzeń produkcyjnych.
3. Koszty ogólnego zarządzania przedsiębiorstwem
- Koszty administracyjne — to np. wydatki związane z funkcjonowaniem biur, zarządzaniem kadrami, usługami prawnymi i innymi funkcjami administracyjnymi.
- Koszty sprzedaży i marketingu — choć nie są bezpośrednio związane z produkcją, są niezbędne dla promocji produktu i jego późniejszej sprzedaży.
Kalkulacja kosztów bezpośrednich
Aby obliczyć koszty bezpośrednie wytworzenia produktu, ważna jest kalkulacja kosztów materiałów bezpośrednich oraz pracy bezpośredniej.
Koszty materiałów bezpośrednich oblicza się, sumując wydatki na wszystkie surowce i komponenty konieczne do wyprodukowania jednostki produktu.
Przy kalkulacji materiałów bezpośrednich należy określić liczbę (ilość) wszystkich surowców i materiałów wykorzystanych do produkcji.
Następnie, aby dokonać dokładnej wyceny trzeba pomnożyć ilość potrzebnego materiału przez jego jednostkową cenę zakupu, uwzględniając ewentualne rabaty lub zmiany cen. Lub odwrotnie, jeżeli dany surowiec i materiał wystarcza do wyprodukowania więcej niż jednego produktu, należy zsumować koszty wykorzystanych materiałów, a następnie podzielić przez liczbę wyprodukowanych gotowych produktów.
Koszty pracy bezpośredniej dotyczą wynagrodzeń i innych kosztów związanych z pracownikami bezpośrednio zaangażowanymi w proces produkcyjny. Obliczenie tego składnika kosztów wytworzenia wymaga obliczenia stawki godzinowej i ustalenie wynagrodzenia za godzinę dla każdego pracownika lub grupy pracowników zaangażowanych w produkcję. Następnie należy określić czas potrzebny na wykonanie jednej jednostki produktu. Dalej należy pomnożyć stawkę godzinową pracownika przez ilość godzin pracy potrzebnych do wyprodukowania jednej jednostki produktu. Należy także uwzględnić dodatkowe koszty pracy, takie jak składki na ubezpieczenia społeczne, które są częścią kosztów pracy.
W rejestracji danych potrzebnych do wytworzenia jednostkowego produktu, czyli zużytych materiałów oraz określenia czasu pracy pracowników biorących udział w produkcji pomoże Ci system enova365 moduł Produkcja.
Kalkulacja kosztów pośrednich produkcji
Obliczenie kosztów pośrednich może nastręczać nieco większych problemów. Nie wszystkie koszty pośrednie wytworzenia produktu są oczywiste — bo nie są bezpośrednio związane z produkcją pojedynczej jednostki produktu.
Aby je obliczyć trzeba wziąć pod uwagę:
- koszty utrzymania maszyn i urządzeń,
- koszty energii i mediów,
- wynagrodzenia personelu pomocniczego,
- koszty dzierżawy i amortyzacji budynków.
Kalkulacja kosztów pośrednich produkcji wymaga zastosowania metody alokacji kosztów, która umożliwia rozdzielanie tych wydatków pomiędzy różne produkty lub linie produkcyjne. Jak wygląda taka kalkulacja?
Krok 1: Zbieranie danych o kosztach
Dokładne monitorowanie i rejestrowanie wszystkich kosztów pośrednich związanych z procesem produkcyjnym.
Krok 2: Wybór bazy alokacji
Ustalenie odpowiedniej metody alokacji kosztów pośrednich. Może być oparta na czasie pracy maszyn, zużyciu energii, powierzchni zajmowanej przez linie produkcyjne lub innym wskaźniku, który najlepiej odzwierciedla sposób, w jaki poszczególne produkty korzystają z zasobów.
Krok 3: Alokacja kosztów
Rozdzielenie zgromadzonych kosztów pośrednich między poszczególne produkty lub linie produkcyjne zgodnie z wybraną bazą alokacji. Na przykład, jeśli bazą alokacji jest czas pracy maszyn, całkowite koszty pośrednie zostaną podzielone proporcjonalnie do czasu, jaki każdy produkt spędza na maszynach.
Warto regularnie aktualizować kalkulację kosztów pośrednich, aby w razie konieczności dostosować koszt wytworzenia produktu.
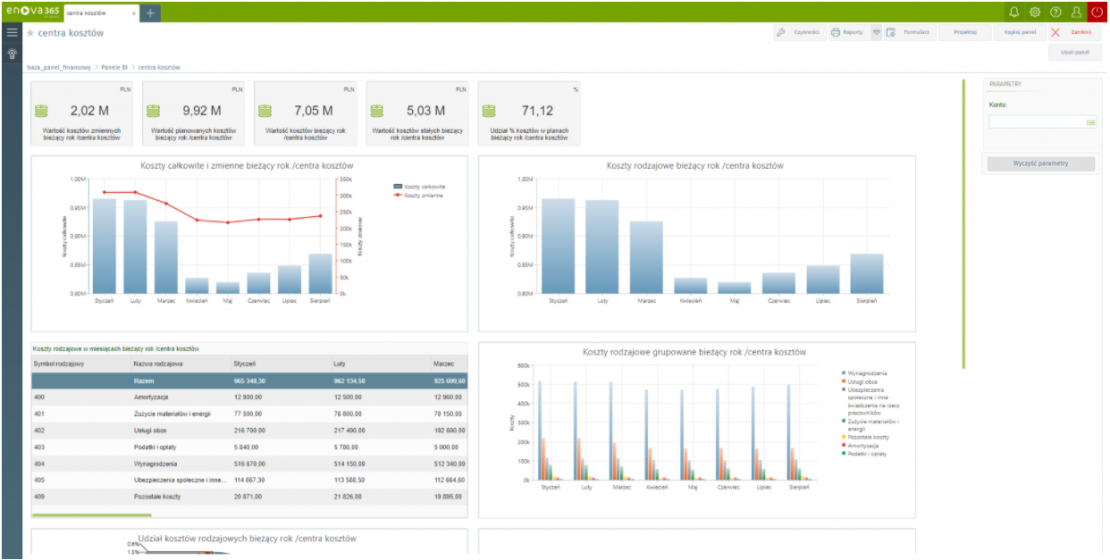
Jak technologia może pomóc w kalkulacji kosztów?
Nowoczesne systemy ERP (Enterprise Resource Planning) integrują dane z różnych działów i procesów biznesowych (sprawdź co to jest system ERP). Dzięki temu można w łatwy sposób zidentyfikować i wyliczyć dokładne koszty produkcji. ERP często umożliwia automatyczne śledzenie i alokację kosztów, od zakupu surowców po koszty pracy i pośrednie. To znacznie ułatwia dokładne obliczanie kosztów wytworzenia produktów.
ERP daje także możliwość automatyzacji obliczeń kosztów. Dzięki temu przedsiębiorstwo może szybko dostosować się do zmian w procesach produkcyjnych czy cennikach surowców. Systemy te mogą również automatycznie aktualizować koszty w odpowiedzi na zmiany w cenach materiałów, stawkach wynagrodzeń czy zużyciu energii.
Zaawansowane narzędzia analityczne i moduły raportujące dostępne w nowoczesnym oprogramowaniu umożliwiają głęboką analizę kosztów i identyfikację potencjalnych obszarów oszczędności. Przedsiębiorstwa mogą korzystać z dynamicznych raportów i dashboardów, aby na bieżąco monitorować wskaźniki efektywności i dokonywać informowanych decyzji strategicznych.
Takie możliwości zapewnia Ci m.in. enova365.
Podsumowanie
Wyliczenie jednostkowego kosztu wytworzenia produktu ma niebagatelne znaczenie dla rentowności przedsiębiorstwa. Powinien być on m.in. podstawą do określenia ceny sprzedaży.
Warto pamiętać, że koszty wytworzenia produktu nie są stałe. Mogą dynamicznie się zmieniać wraz ze zmianami w cenach surowców czy kosztów pośrednich, np. cen energii elektrycznych czy kosztów transportu.
Aby obliczyć koszt wytworzenia jednostkowego produktu, warto wykorzystać odpowiednie oprogramowanie, które pomaga monitorować czynniki wpływające na produkcję, np. czas pracy pracowników, wykorzystanie maszyn czy ilości surowców potrzebnych na linii produkcyjnej. Nieoceniona okazać może się tu enova365, moduł Produkcja.
Umów się na prezentację i sprawdź, jak enova365 usprawni funkcjonowanie Twojej firmy. Przetestuj system i pobierz 14-dniowe bezpłatne demo.
Bibliografia
- https://mfiles.pl/pl/index.php/Koszt_wytworzenia_produktu
- https://dok.enova365.pl/Topic/36422,
- https://dok.enova365.pl/Topic/38358
- https://dok.enova365.pl/Topic/38432
- https://dok.enova365.pl/Topic/38679